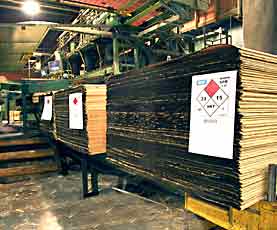
Increased Dryer Productivity
The most important measure for any new technology is the bottom-line impact. While all inventory management systems will add operational improvements, it is often challenging to quantify the incremental productivity increases and derive a concrete dollar value for ROI (return on investment) analysis.
On the surface, the LightMARKTM system may appear to be little more than a simple inventory management tool. However, the real opportunity for bottom-line impact comes from increased dryer productivity. By harnessing stack data generated by the LightSORTTM and integrating this into your drying process, you can gain greater control of the drying process, and realize the productivity impacts of this increased level of control. Some of the opportunities are outlined here, but these are not the only possible scenarios. You may find other ways to put the LightSORTTM information to work to optimize your green-end production.
Load Matching
Perhaps the most immediate way to increase dryer productivity can be realized through simple "load matching". Stacks with identical or similar moisture content are run through the dryer together.
Because the moisture content remains relatively homogenous across the length and width of the dryer, controller tracking is steady and consistent. The potential for controller overshoot and oscillation is drastically reduced. Veneer quality is improved with less redry and more in-target MC (moisture content) veneer.